Wind Turbine Blades Design and Analysis
- Mukesh Dewangan
- Jan 9, 2017
- 2 min read
The need for making wind turbines more efficient is an ongoing tasks and to optimize or limit the power extracted from the wind turbine is controlled by rotor’s rotation speed and the pitch of the blades. Recently, an increasing concern has been given to Morphing Blades. It is well known that Morphing Blade’s power efficiency can be improved by changing their shape accordance to the wind direction and speed. Moreover, it can be done with a potential to significantly relieve unwanted stresses to prolong their life when the wind gets severe on it. In this project, I developed a simple interlocking system to achieve it in Catia V5, the NACA airfoil coordinates are used for designing the morphing blade.
Different design are proposed and comparison of axiomatic diagram are made with different functional requirement and design parameters by using octopus and fast diagram as shown below.

To choose the best design the Morphing blade is divided into nine different section where each three section belongs to NACA airfoil as shown in fig (2) and the joint between the section is provided by high modulus elastomer which also provide each section a necessary twist angle. Designing, Simulation and analysis is done with the help of CATIA V5.

Fig 2. Best Axiomatic Design
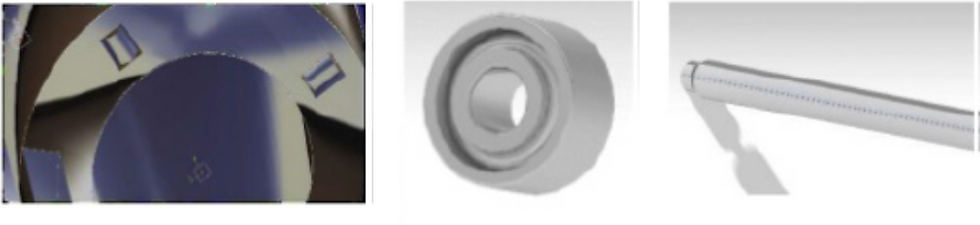
Fig 3. Solid / Part Modeling
Assembly i.e. Motor assembly, Gear assembly and surface rollers, bearing, blade skin section at appropriate position and degree of freedom are show in fig 4. Simulation of gear assembly, motors and airfoils are also shown in figure below.

Fig 4. Assembly
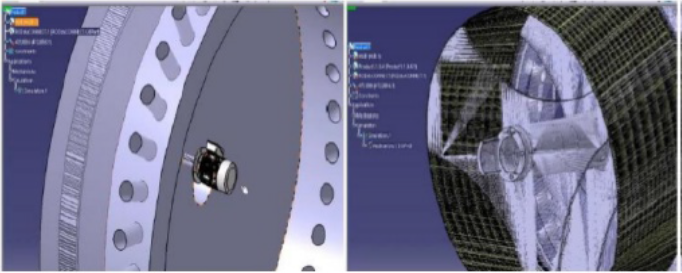
Fig 5. Simulation of Gear Assembly
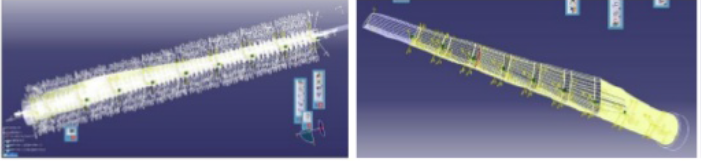
Fig 6. Simulation of Motors and Airfoils


Fig 7. Surface Analysis of Section and Blades
The total mechanism is driven by the high torque step motors which works on inputs by the wind sensor, depending on wind the motors drives the section to get necessary drag for more efficiency. This motor with the gear assembly is attached with the hub that does not have the twist moment. Each Morphing blade has its own motor yet the inputs are synchronized.

Fig 8. Mechanism Fig 9. Detailed Drawing
Comentarios